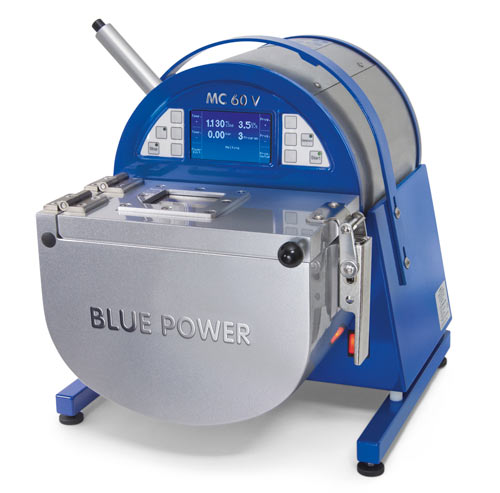
Overview MC 60 V
The tabletop casting machine MC 60:
The compact solution for small series casting in aluminium, copper, brass, zinc, brass, gold and silver
- New: Run of process with controller
- New: LCD-display with all program data
- New: Vibration system for optimized form filling
- Graphite crucible, temperature up to 1300° C
- Very simple use, short training period, very good results even by operators with less experience in casting techniques
- Excellent price-performance ratio
- 3,5 kW generator enables quick melting periods
- Thorough mixing of metal by induction generator (low frequency tuning)
- Melting under vacuum for reduced danger of oxidation
- Excellent mould filling because of inert gas / over-pressure, max. 2 bars
- Low running costs because of inexpensive consumables and the use of flasks without flange
More about MC 60 V
Rapid and simple casting
The MC 60 V has been developed with the user in mind for whom the MC 16 is too small but a simple machine from the large VC series (e.g. the VC 400) is too big or requires too much manual operation. This small high-performance casting machine is ideal for smaller production quantities and can be used for jewellery alloys such as gold, silver, copper and bronze, as well as for alloys of brass and aluminium.
The whole process of casting can be carried out simply, quickly and safely without any real prior technical knowledge of casting. With the MC 60 V – and with all MC machines – you can easily cast by hand from the crucible to your mould and feel what you are doing – just as it has been done for thousands of years. So that this works consistently and safely, the entire melting/casting unit is tilted together through a 90° angle. For perfect balance and to make do with as few moving parts as possible, almost the whole machine moves during tilting: being cylindrical in design, the whole moving section rotates as if in a halfpipe – ingeniously simple and stylishly designed on high-quality rollers. However, unlike manual casting, the process takes place in an enclosed chamber under a vacuum or inert gas atmosphere, to prevent air pockets and oxidation. You can check the melting and pouring-off process through the sight glass.
Main benefits
- Now with program control and LCD display
- Vibration system for optimized form filling
- Very simple use, short training period, very good results even by operators with less experience in casting techniques
- Excellent price-performance ratio
- 3,5 kW generator enables quick melting periods
- Thorough mixing of metal by induction generator (low frequency tuning)
- Melting under vacuum for reduced danger of oxidation
- Excellent mould filling because of inert gas / over-pressure, max. 2 bars
- Low running costs because of inexpensive consumables and the use of flasks without flange
Technical data MC 60 V
power | |
power max. / electrical connection | 3.5 kW 230 V single phase |
temperature max. | 1300° C |
capacity | |
casting volume | 260g Cu |
for flask size | ø 100 mm x 120 mm H |
handling and control | |
control panel | LCD display |
automatic vacuum function | |
automatic overpressure function | |
casting also under vacuum only | |
vacuum or overpressure after casting | -1 up to +2 bar |
washing by inert gas | |
vibration system | |
supply: cooling water, inert gas argon or nitrogen | |
temperature measurement/control | up to 1.300° C |
quality control | |
RS 232, diagnostic system | |
GSM modem for remote service | |
accessories | |
vacuum investment mixer Indumix 2 | |
furnace AK 20, 1100°C | |
sand blasting cabinet | |
vacuum pump | (min. 8m3/h) |
floor unit | |
All machine descriptions and technical data published on this site make no claim to be complete. They are subject to change and therefore they are not basis of contract.