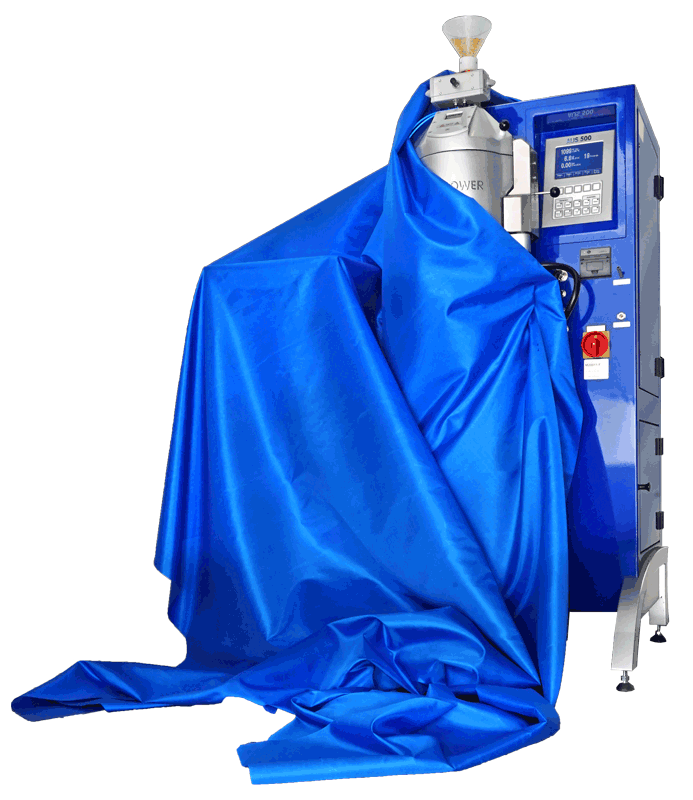
Overview Ultrasonic Atomizer AUS 500
More about Ultrasonic Atomizer AUS 500
Ultrasonic Atomizer Solution by BLUE POWER and AMAZEMET – from alloy creation to powder within 1 hour
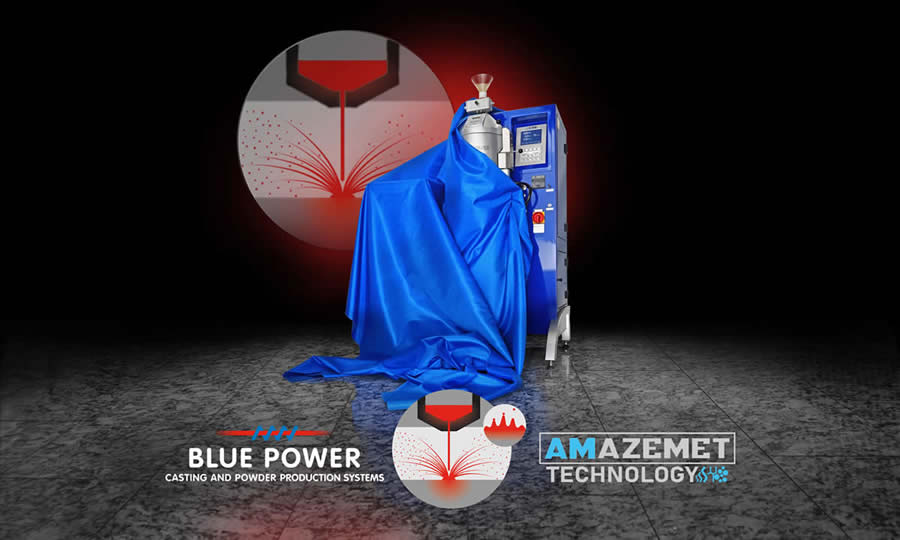
In cooperation with AMAZEMET, a Warsaw University of Technology company, BLUE POWER has developed an extremely compact Ultrasonic Atomization Unit for R&D purposes and small powder batch production. While BLUE POWER has 25 years’ experience in induction melting technology, AMAZEMET provides know-how in Ultra-High Temperature Ultrasonic Technology and materials science in additive manufacturing. The two companies decided to combine their expertise to develop an innovative unit with unique functionalities and profitability. Dr Fischer-Bühner (Head of R&D BLUE POWER) explains, that the Atomizer Unit enables almost anybody to produce small batches of high quality, spherical powder for the same target application as gas atomized powder at an affordable price and without having a complex infrastructure.
BLUE POWER with its 60 service partners all over the world will be taking care of the global distribution, support, and service
Features
- Prevention of material loss and inaccuracy of alloy chemistry due to precise control of melting temperature via crucible based induction heating system, while evaporation of alloy ingredients like Zn, Cr…is a common issue during plasma-assisted atomization.
- No sophisticated and expensive filter required for evaporated alloy ingredients otherwise caused by plasma melting
- Possibility to create own alloy composition inside of the Atomizer’s crucible-based melting system
- Alloying possible with good stirring/mixing effect due to strong medium frequency induction generator
- Controllable atmosphere and melting under vacuum
- Feedstock could be in more or less any shape – not just pre-alloyed wire or bar
- No need of complex and expensive wire production as feedstock material for atomising, which is time consuming and requires additional infrastructure like continuous casting machines, drawing bench…
- No calibration required; pre-installed programs for basic materials / alloys
- Increased yield due to higher frequency of Ultrasonic Technology (e.g. Bronze d50= 40-60 µm)
- Increased production capacity (throughput up to several kg/h Bronze)
- Very small batch sizes down to ~ 100 g technically and financially viable
- The system is designed to work with almost any non-ferrous metal with T < 1300 C (high temperature option up to 1800 is in development).
- Extremely spherical powder without any satellites for highest powder fluidity and bulk density
- Could be basically used as well for non-metallic materials (certain fluidity required)
- Footprint of just a few square meters including infrastructure
- Maximum versatility by using the machine for granulating or ingot casting as an option
- A design for easy handling & cleaning, quick alloy change with minimum cross contamination: The user-oriented and modular structure of the systems ensures optimum accessibility for all work as well as for inspection and maintenance. This construction principle also ensures short installation and training periods.
- Anti-oxidation features: As all AU series machines offer the possibility of oxidation-free processing in the closed-chamber machine by means of de-gassing, vacuum and protective gas features. Oxygen sensor values below 0.5 ppm can be achieved reproducibly.
- Easy-to-clean concept: Polished stainless steel surfaces prevent powder adhesions in spray chamber and collector – all parts are easy to clean without any residues. This way the risk of metal loss and cross-contamination is reduced to minimum.
- Larger version offering a crucible volume of 1.5 l in development!
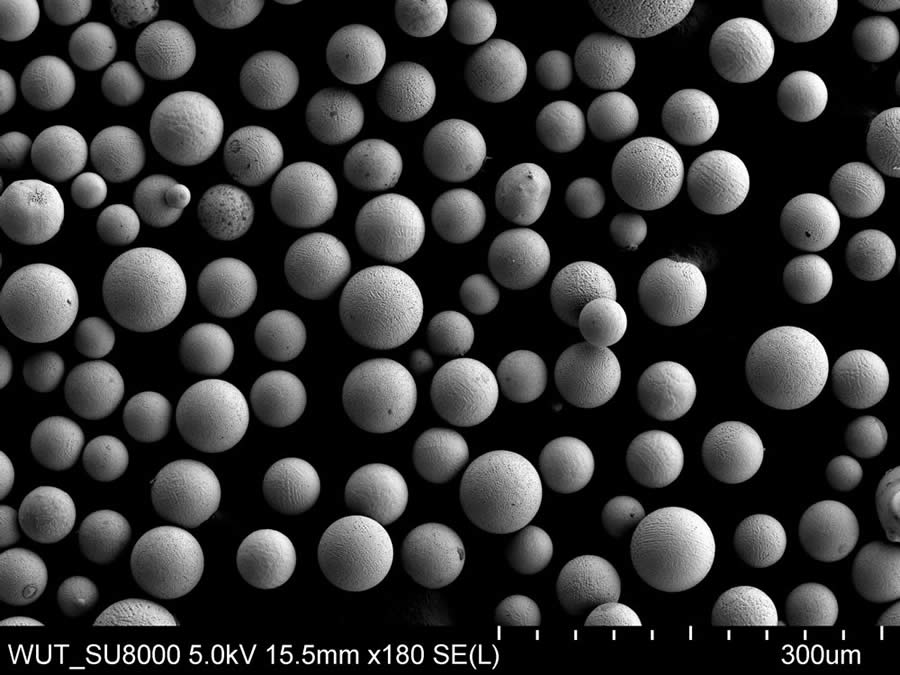