Innovative Solutions for Networking, Data and Process Management in the Foundry
The current crisis has made it clear to all of us how important digitalization and networking are for communication, production processes and the entire value chain. Blue Power has been communicating directly with its customers’ machines for many years for remote maintenance, software updates, assistance and consulting. We have also been providing our customers with a data management system (DMS) for each of our machines free of charge for years, with which casting processes can be logged and analyzed. We have now developed a user-friendly and intuitive system on these foundations for data and process management for our foundry customers.
We use complex control electronics as well as the existing sensors on the casting and powder atomizing machines for data acquisition. This allows numerous parameters to be recorded and processed via sensors, such as power output, temperatures, compression ratios and many more. Every individual (casting) process can be precisely analyzed and saved.
The system consists of individual modules that can be configured according to customer-specific requirements. Depending on the application, the user has various user interfaces available for control and management. After all, information for employees on the foundry shop floor is generally different from that which is relevant for material planning, quality assurance or management.
Fast Access to All Relevant Data – Our System Services at a Glance
The development focused on the following functions:
- Process data output and its visualization (analytics, live views, evaluation)
- Report output (documentation, quality assurance)
- Script control (production control, process control)
- Remote control (process control, process monitoring)
- Statistics (evaluations, efficiency analysis, optimizations)
- Flexible data access including cloud communication (process monitoring, process statistics, process documentation)
- Software updating (maintenance, service)
Three Modules for Customized Solutions
Our data and process management system consists of three tools that can be used independently of one another:
- Indutherm DMS (App, Shell and NEW: Panel)
- NEW: IThermControl
- NEW: Indutherm Cloud
Our System Modules in Detail
The DMS App
Technically, we have been making the DMS app available to our customers free of charge for years. Through continuous further development, we are continuously creating new possibilities for data acquisition, output and visualization to make the production process safer and more efficient. With this tool, software updates can be installed on the system, process logs (printers) can be read, parameters can be read from the system and also tracked live. The raw data output can then be visualized using other tools such as Microsoft Excel etc.
The DMS Shell
DMS Shell offers, for example, higher-level controls, machine parameters and parameters for transfer. The data from upstream or downstream processes can then be processed, documented, displayed, etc.
The new DMS Panel
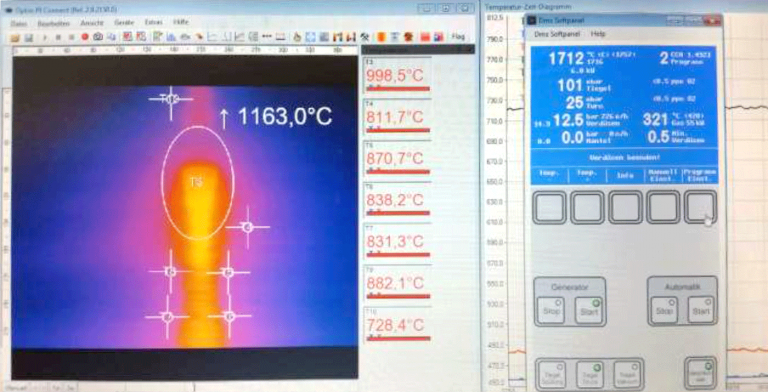
DMS Panel is used to control the machines remotely. The machines can largely be monitored and controlled from a central location, for example from a desk, especially in combination with the various optional (post-) charging systems or with robot systems for changing cuvettes. Since the user interface and functions look identical to the control panel and the display of the associated machine, operation via DMS Panel appears familiar from the very start.
IThermControl
IThermControl is a local software solution for the optimization of processes, report output (documentation), process monitoring, live views, visualization and documentation. A statistics function has also been added, which shows, for example, how many batches or how many meters of tube, etc. the machine has produced per unit of time. Basically, it overlaps the functions of the DMS solution for parameter output. However, IThermControl can visualize the data directly and display it in statistics, among other things. The software is installed and managed on the customer’s company network. With the option of a customized display, each user has the option of displaying information that is of interest to them. This view configuration can, of course, be saved or changed at any time.
InduthermCloud
The new Indutherm Cloud is based on IThermControl in terms of functionality and options but is a web-based solution that, with the appropriate access authorization, enables data access from anywhere in the world with an Internet-enabled device (PC, laptop, tablet, smartphone, etc.).
Using IoT technology, the data is transferred to a cloud, in which it is not only stored, but also visualized and processed. With appropriate access information, the user can call up system statuses in real time as well as historical data from anywhere in the world with any device via the Internet. Various masks are available for this to provide the appropriate information in a way that suits each individual. The advantages of this solution are flexible access and that the entire infrastructure is outsourced. No expensive servers or IT experts are required to manage the hardware.
Alternatively, as shown above, a solution is available that is installed locally or in the company network: Similar to the cloud solution, “IThermControl” offers an automated display of the current system status and process history.
For more information, please contact us This email address is being protected from spambots. You need JavaScript enabled to view it.