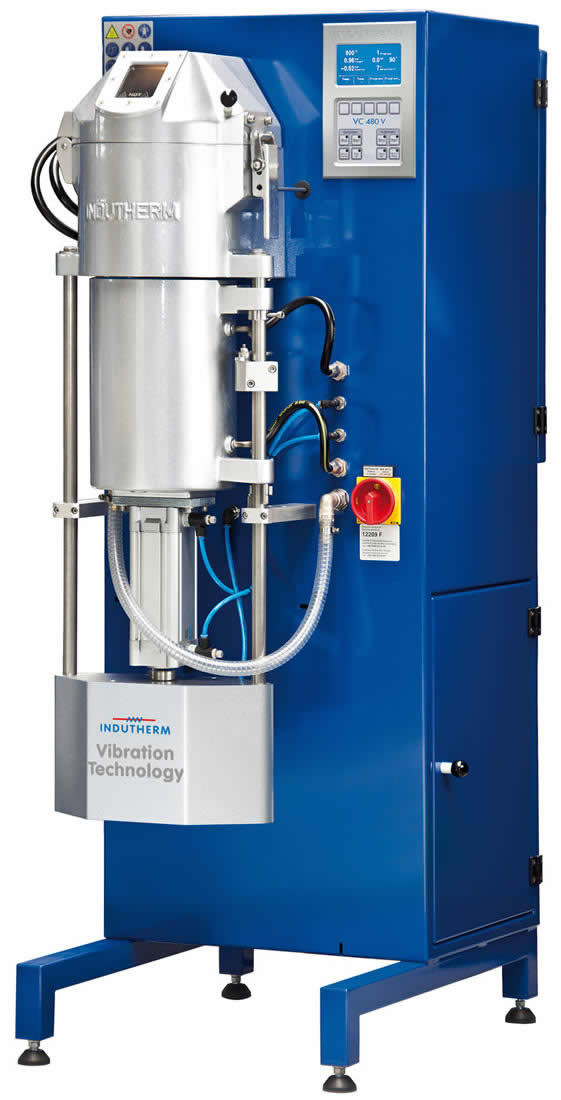
Overview VC 480 V Vacuum Pressure Casting Machine
Vibration technology now also in the mid-size class: the highly economic vacuum pressure casting machine VC 480 V
Equipped with the INDUTHERM Vibration System for optimized form filling and castings with reduced porosity, finer grain and optimum post-processing properties. 8 kW induction generator, variable vacuum in the flask chamber. Crucible volume max. 170 ccm = 2,5 kg Au 18 ct Flask size Ø 130 mm x H 260 mm Temp. max 1.600° C
Download technical data [PDF]More about VC 480 V Vacuum Pressure Casting Machine
New programm control system
Thanks to a new control panel with real text LCD display, all programs and parameters are very easy and comfortable to set.
100 casting programs guarantee fast operation and consistent casting results.
Turbulence reduction software
This is a new system for a faster and more laminar metal flow.
The Indutherm Vibration System
The vibration technology (pat. pending) is the most important of all technical features. Independent scientific studies show that:
- Vibration improves material flow and hence the quality of the mould filling, particularly with complicated moulds.
- Castings exhibit a higher and more consistent density for all tested alloys and shapes.
- Porosity is substantially reduced.
- Risk of hot cracks is reduced.
- 50% smaller grains
- Castings have greater stress and elasticity properties, making them easier to process further.
In practice this means:
higher and more consistent casting quality, less waste, less post-processing, more possibilities for further processing.
Technical data VC 480 V Vacuum Pressure Casting Machine
power | |
power max. / electrical connection | 8 kW 3x400 V |
temperature max. | 1600° C |
capacity | |
crucible volume | 170 ccm = 1,5 kg Cut * |
for flasks up to | ø 130 mm / 240 mm H |
handling and control | |
vibration technology | |
pneumatic bell lock | |
oberpremssure max. | 1,5 bar |
programs | 100 |
dual temperature control | |
flask temperature measurement | |
flask lift | |
variable vacuum in the flask chamber | |
Turbo Pressure PLUS system | |
Turbulence Reduction Software | |
quality management | |
RS 232, diagnostic system | |
data printer | |
GSM modem for remote service | |
accessories | |
sinter kit (for diffusion bonding) | |
granulation tank | |
* liquid metal up to top level of the flask | |
All machine descriptions and technical data published on this site make no claim to be complete. They are subject to change and therefore they are not basis of contract.