Blue Power Induction
INDUTHERM machines are suitable to melt and cast metals of high melting temperature. According to the model, they can also melt steel. Also alloys or metal with a low melting point such as Aluminium may be easily processed with them.
Operation principle of our Vacuum Pressure Casting Machines:
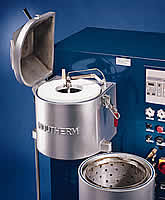
The basic idea of the INDUTHERM vacuum/pressure casting machines is to close the cover and start the heating up once the machine has been filled with casting material.
The temperature may be selected by hand or it may be programed depending on the model you are working with.
The material is molten under protective gas to avoid oxidation. The melting procedure may be observed through the viewing window. The crucible is placed centrally in the upper part of the air-tight closed aluminium case in the core of the induction spool.
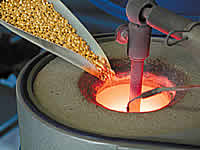
In the meantime the flask with the heated up casting form is placed in the lower part of the aluminium case (vacuum chamber). The vacuum chamber is tilted and docked under the crucible. For the casting process the crucible is set under pressure and the flask under vacuum. The difference of pressure leads the liquid metal into the finest ramification of the form.
The vacuum avoids bubbles and porosity.
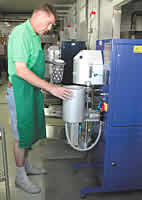
Afterwards the vacuum chamber is opened and the flask may be removed.
Most machines are equipped with a flask lift which pushes the flask towards the caster. This simplifies the removal of the flask.
Additional possiblities:
- Production of alloys
- Granulating (with an additional granulating flask)
- Casting of ingots – instead of a flask an ingot form has to be inserted
- Sintering/Diffusion welding: with the sinter-kit all Indutherm vacuum/pressure casting machines may be used for sintering

Anyone who relies solely on high performance manufacturing casting machines is usually thinking too narrowly.
What matters most is what is accomplished with each kilowatt hour consumed. The induction generators and inductors in our casting and melting machines are designed with the highest possible level of energy efficiency. Sophisticated insulation ensures that the induction generated loses as little energy as possible for fast melting of the metal.
The thermal insulation around the inductor and crucible effectively reduces heat radiation; the entire melting chamber and drum act like a Faraday cage to prevent the radiation of electromagnetic waves.
Also the infused stainless steel coolant water lines further improve the shielding effect. With open melting machines that cannot use the ‘cage effect’, the radiation loss is reduced almost as effectively through the use of ring-shaped ferrites – and at the same time the electrosmog load for users is drastically reduced.
Indutherm machines with energy efficiency
Thanks to the flask lift you can use flasks with no flange, offering two ways to save money: flangeless flasks are much cheaper and require ~60% less space in your oven (compared to 10 cm diameter flasks with and without flange).
In other words: with energy efficiency the same energy consumption you can burn up to 60% more flasks – or you can work with a smaller oven.
Innovative Solutions for Networking, Data and Process Management in the Foundry
The current crisis has made it clear to all of us how important digitalization and networking are for communication, production processes and the entire value chain. Blue Power has been communicating directly with its customers’ machines for many years for remote maintenance, software updates, assistance and consulting. We have also been providing our customers with a data management system (DMS) for each of our machines free of charge for years, with which casting processes can be logged and analyzed. We have now developed a user-friendly and intuitive system on these foundations for data and process management for our foundry customers.
We use complex control electronics as well as the existing sensors on the casting and powder atomizing machines for data acquisition. This allows numerous parameters to be recorded and processed via sensors, such as power output, temperatures, compression ratios and many more. Every individual (casting) process can be precisely analyzed and saved.
The system consists of individual modules that can be configured according to customer-specific requirements. Depending on the application, the user has various user interfaces available for control and management. After all, information for employees on the foundry shop floor is generally different from that which is relevant for material planning, quality assurance or management.
Fast Access to All Relevant Data – Our System Services at a Glance
The development focused on the following functions:
- Process data output and its visualization (analytics, live views, evaluation)
- Report output (documentation, quality assurance)
- Script control (production control, process control)
- Remote control (process control, process monitoring)
- Statistics (evaluations, efficiency analysis, optimizations)
- Flexible data access including cloud communication (process monitoring, process statistics, process documentation)
- Software updating (maintenance, service)
Three Modules for Customized Solutions
Our data and process management system consists of three tools that can be used independently of one another:
- Indutherm DMS (App, Shell and NEW: Panel)
- NEW: IThermControl
- NEW: Indutherm Cloud
Our System Modules in Detail
The DMS App
Technically, we have been making the DMS app available to our customers free of charge for years. Through continuous further development, we are continuously creating new possibilities for data acquisition, output and visualization to make the production process safer and more efficient. With this tool, software updates can be installed on the system, process logs (printers) can be read, parameters can be read from the system and also tracked live. The raw data output can then be visualized using other tools such as Microsoft Excel etc.
The DMS Shell
DMS Shell offers, for example, higher-level controls, machine parameters and parameters for transfer. The data from upstream or downstream processes can then be processed, documented, displayed, etc.
The new DMS Panel
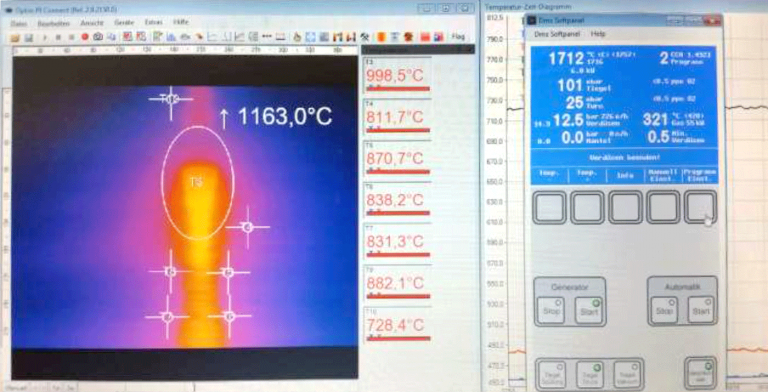
DMS Panel is used to control the machines remotely. The machines can largely be monitored and controlled from a central location, for example from a desk, especially in combination with the various optional (post-) charging systems or with robot systems for changing cuvettes. Since the user interface and functions look identical to the control panel and the display of the associated machine, operation via DMS Panel appears familiar from the very start.
IThermControl
IThermControl is a local software solution for the optimization of processes, report output (documentation), process monitoring, live views, visualization and documentation. A statistics function has also been added, which shows, for example, how many batches or how many meters of tube, etc. the machine has produced per unit of time. Basically, it overlaps the functions of the DMS solution for parameter output. However, IThermControl can visualize the data directly and display it in statistics, among other things. The software is installed and managed on the customer’s company network. With the option of a customized display, each user has the option of displaying information that is of interest to them. This view configuration can, of course, be saved or changed at any time.
InduthermCloud
The new Indutherm Cloud is based on IThermControl in terms of functionality and options but is a web-based solution that, with the appropriate access authorization, enables data access from anywhere in the world with an Internet-enabled device (PC, laptop, tablet, smartphone, etc.).
Using IoT technology, the data is transferred to a cloud, in which it is not only stored, but also visualized and processed. With appropriate access information, the user can call up system statuses in real time as well as historical data from anywhere in the world with any device via the Internet. Various masks are available for this to provide the appropriate information in a way that suits each individual. The advantages of this solution are flexible access and that the entire infrastructure is outsourced. No expensive servers or IT experts are required to manage the hardware.
Alternatively, as shown above, a solution is available that is installed locally or in the company network: Similar to the cloud solution, “IThermControl” offers an automated display of the current system status and process history.
For more information, please contact us This email address is being protected from spambots. You need JavaScript enabled to view it.
The induction principle is optimal for melting metals. The crucible is positioned in the core of the induction coil so that a steady temperature can be directly generated in the melting material. Because of the strong magnetic field the liquid metal will be mixed intensively. The so-called inductive bath movement makes the production of pre-alloys unnecessary.
- All Indutherm induction generators are:
- our own developments
- optimized for each machine
- absolutely reliable for steady state
- easy in service
- particularly designed for low frequency applications and therefore excellent stirring of the metal
- use a RS 232 PC interface and Software
- and as a brand new option we can control and supervise the machines directly from our office by using a GSM modem